Digital Machinery Decoded
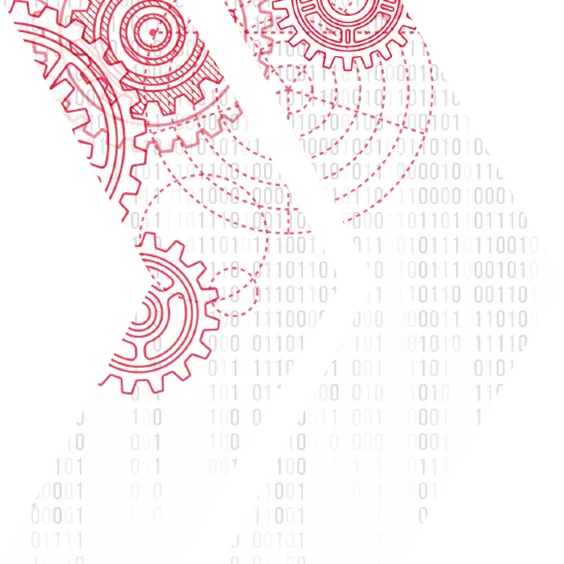
A practical guide for machinery companies to navigate digital transformation and outperform competition
Porsche Consulting surveyed 50 machinery companies from Germany, Italy and Switzerland as part of a new study on the digital transformation. The findings: In recent years, the focus of digital transformation in machinery was still being directed at efficiency gains. This has since been supplanted by a focus on the growth opportunities being created by new digital products and digital services, as well as the changes to customer relationships in multi-channel markets and customer service. Although two-thirds of the companies surveyed said they would undertake digital activities geared toward growth, efficiency and the customer experience, 88 per cent have become, and will remain, stuck by the time they reach the pilot phase. Company-wide implementation is a rarity.
In the study entitled “Digital Machinery Decoded”, management consultants at Porsche Consulting analyzed how companies can capitalize on the potential of the Industrial Internet of Things more holistically and more sustainably. They also examined how machinery engineers can improve their customer relationships by means of e-commerce and new methods of interaction, while simultaneously stimulating their after-sales business. The Porsche consultants highlight how companies can shape their digital transformation, and achieve digital success more quickly
Read the whole study now
You want to get in touch with our experts? Reach out to us.